根据美国堪萨斯大学的研究(图1),影响颗粒料品质的各个因素中,饲料配方占40%、粉碎占20%、调质占20%、制粒机及环模压辊占15%,冷却占5%。而在影响饲料厂颗粒产量的各个因素中,饲料配方占40%、调质占25%、制粒机及环模压辊占25%,粉碎占10%。
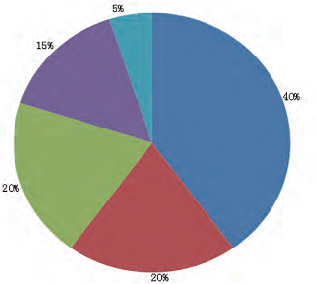
3.1 调质三要素
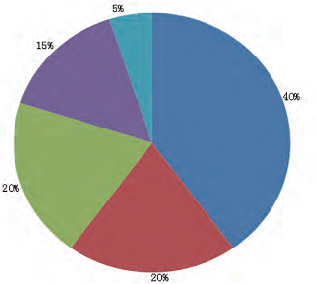
图 1 影响饲料颗粒品质的因素及权重比例
1 配方
在竞争日趋激烈的今天,决定饲料厂成败的关键往往就是2%~3%的利润,所以配方师设计配方时,应从经济性和市场性的原则考虑,因地制宜、因时制宜,用最低最合理的当地配方资源来满足畜禽最基本的需求。
从原料的特性及其选择来看,必须要考虑到饲料生产加工工艺的可行性,生产员工的可操作性,以及配方中涉及的原料对颗粒品质的影响。譬如在调质过程中,淀粉会吸收蒸汽的热量和水分,发生糊化反应,交联物料各组分并对饲料颗粒成型有促进作用。而物料中适宜含量的天然蛋白质在水和热量的作用下具有良好的可塑性,有利于颗粒品质。但是,蛋白质的变性过程是疏水过程,日粮中过多的蛋白质不利于物料对蒸汽水分的吸收,从而影响调质效果。另外,配方中的脂肪添加也不利于颗粒品质的塑造,会导致饲料颗粒容易粉化。所以就如何塑造理想的颗粒品质,特别是对于禽料、水产料等,配方设计过程中需要充分考虑原料特点及其对颗粒品质的影响。
2 粉碎
粉碎越细,比表面积越大,能快速吸收更多的蒸汽,颗粒含粉少,颗粒质量更好,对制粒机环模压辊的磨损少、产量高。粉碎不好的物料,颗粒含粉多、品质差、成品颗粒长短不齐、有凸凹料,易断裂。
从颗粒质量方面来考虑,粉碎的越细越好。但是从经济效益的角度考虑,过细的粉碎会造成电耗过高,畜禽生产线粉碎电耗占到总电力消耗的40%左右,水产尤其虾料生产线电耗占到60%左右。另外,粉碎工艺是饲料生产中水分损耗最大的环节,如水分为14%的玉米,用2.5mm 筛片粉碎后,水分散失约0.8%,水分为15%的玉米,水分散失约1.2%,而这部分损耗是饲料厂目前无法解决的问题。所以,要从客户需求来综合考虑粉碎粒度。
3 调质
笔者从事饲料行业20多年,非常认可这样的一个观点:“影响饲料颗粒质量的第一位点是调质。”调质就是所有物料进入混合机到制粒机环模腔之间所有的添加和改变。而饲料厂选址建成后,在固定成型的饲料生产工艺过程中,影响颗粒料品质因素中的 60% 在进入混合机之前就已经固定,我们所能做的最重要改变就是调质的 20%,而这 20%恰恰是生产中原料向饲料完成质变转换过程的最关键步骤。
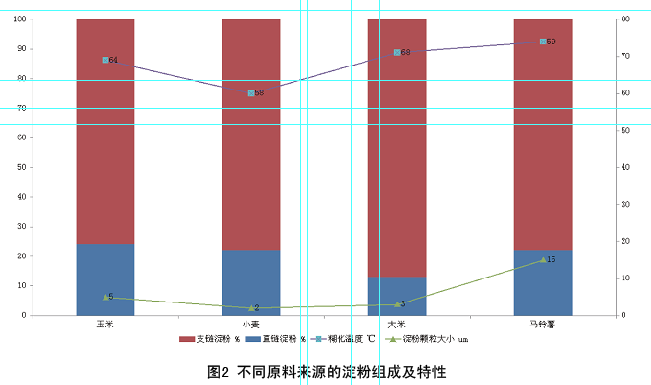
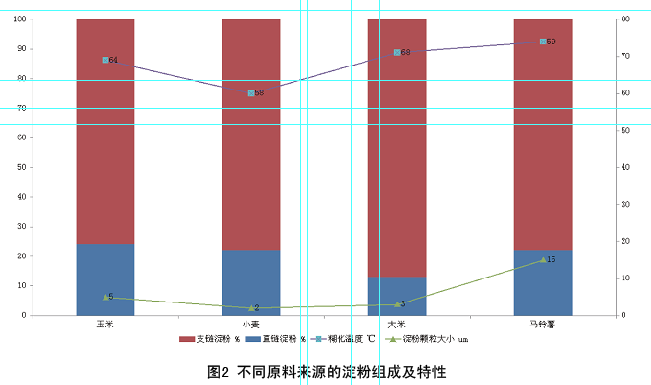
3.1 调质三要素
3.1.1 时间 取决于调质器的型式。调质时间越长,蒸汽与粉状饲料的接触混合时间越多,添加的蒸汽量越多,越有利于畜禽饲料的淀粉糊化、水产饲料的蛋白质变性。通过调整调制器的叶片角度来加长调质时间,高谷物畜禽饲料调质时间应该在40s以上,调整叶片角度以调质器电机电流控制到额定电流内不跳闸为最大调整角度。
3.1.2 温度 饲料厂设计之初,通常会先按照 75kg/t的蒸汽标准来选择锅炉,实际制粒消耗的蒸汽量可以按照50kg/t 来计算。畜禽颗粒料的制粒温度在78~83℃之间,目的是淀粉糊化和杀灭有害菌,玉米、小麦、薯类等淀粉类原料的糊化温度在58~72℃(图2),要用饱和蒸汽,经减压阀后蒸汽压力最好在2.5kg/cm2左右,要确保蒸汽系统汽水分离器、疏水阀工作正常,避免因含水蒸汽进入调制器而造成湿堵机故障。水产颗粒料的制粒温度要在90℃以上,目的是蛋白质变性及灭菌,蒸汽压力可以选用4kg/cm2左右。
锅炉的蒸汽压力通常为7~8kg/cm2,蒸汽输送采用高压输送,低压使用,降低输送损耗。压力越高、蒸汽含水越少、压力越低,蒸汽含水越多。
3.1.3 水分 在影响颗粒料品质的因素中,调质最重要,而在影响调质的因素中,吸水比吸热更重要,由此可见,水分在影响颗粒料品质的因素中尤为重要。
调质的最佳水分为15%~16.5%,影响调质水分的最大原因是原料的水分。对于大多数饲料厂每年至少在 6 个月以上的,成品颗粒料水分都达不到配方师设计的水分要求,畜禽颗粒饲料水分通常在11%左右,沉水鱼料水分更低,甚至在 9% 左右。由此导致物料淀粉糊化不足,饲料含粉增加,严重影响畜禽的饲料转化率,特别是幼龄畜禽的营养利用率。
部分饲料厂采用在混合机里面加水的办法来寻求解决方案,但是这部分增加的水分是游离水,同时保水率也很差。譬如在混合机里面添加1%的水,成品保留率只有0.25%左右,假如我们希望提高1% 的成品颗粒水分,则需要添加约30~40kg水/t饲料,这样不仅会引发生产中的制粒堵机的问题,而且有很大的霉变风险。
所以,要想提高调质水分,在混合机里面加水必须以保证饲料安全为前提。笔者采取液体防霉剂与水混合后添加到混合机里,来解决调质水分不足的问题 ( 表1)。

3.2 如何解决调质水分问题,做到既防霉又保水
在调质过程中,蒸汽的添加是非常重要的,很多饲料厂生产人员对此的重视程度远远不够。为达到较好的调质状态,必须添加足够高质量的蒸汽,通到调质器的蒸汽应使用调压装置以保持蒸汽压力的恒定。为了提供高质量的蒸汽,汽水分离器、疏水阀、适当的管道尺寸都是必需的,在蒸汽管线靠近调质器的位置,应去除蒸汽中的冷凝水,防止过多的水进入调质器,避免因此而造成的堵机或者霉变等问题。
向调质器里面喷水来调整调质水分是非常错误的做法。调质器不是混合机,添加水分的保留幅度一般不会超过0.5%,并且会严重破坏调质器内蒸汽的添加环境,同时添加水分的不均匀,造成局部水分偏高,生产上容易引起制粒机堵机,而在长江以南地区又极易发生霉变。
目前,最好的水分优化控制系统(设备)是全自动在线水分控制系统,采用微波技术实时高频率扫描混合仓物料水分,根据物料水分实际值与目标值的设定,自动配置液体防霉剂与水的混合液,并通过雾化定量向混合仓内的物料喷涂。该系统可以实时在线,全天候远距离监测并控制物料水分,能够执行任何水平的调质水分及成品颗粒饲料水分。
而当前主流的水分控制系统是称重型传感器系统,称重静态精度0.2%,动态精度0.5%,每批次自动配料并混合添加,根据原料水分来可以设置不同配方,能够将成品颗粒水分稳定控制在12.5% 左右。
另外在市场上,有部分企业会采用流量计控制系统,该类型设备系统投资较低,精度较差,采用国产流量计的设备精度通常在2%左右,水分添加误差大。在每批配料过程中,容易造成液体防霉剂和水出现分层现象。很容易造成霉变事故或导致饲料适口性变差。
液体防霉剂一定要选大品牌。配套的添加设备及有关工艺也很重要,用得好,可以提高淀粉糊化度,降低含粉率,改善适口性,提高生产效率,同时,由于粉状饲料的润湿和软化,制粒时耗电量降低;用得不好,反而导致设备故障、饲料霉变和客诉的增加。
4 环模和压辊
环模对颗粒料品质的影响主要是环模的压缩比、孔径、减压孔直径及深度、环模日常保养及环模壁的光滑程度。要保证颗粒饲料质量,对不同品种的饲料要选用不同压缩比及孔径的环模,每次制粒结束后必须用含油料清洗环模,避免环模内壁因腐蚀而变得粗糙。环模入料口内凹、环模内壁粗糙、划痕等因素必然造成颗粒品质下降。饲料颗粒表观质量的要求是颗粒长短度、光滑度、含粉率、硬度、耐水性、颜色、水分等。其中,压缩比是一个极为重要的因素,不同品种颗粒饲料,猪、肉禽、沉水鱼、虾蟹等对压缩比的要求也不同,譬如教槽乳猪料对硬度敏感,肉禽料对含粉率要求高,水产料对耐水性有特别要求等。应根据具体的料型、客户的需求以及原料的多样性来确定压缩比,有时需要牺牲产量来追求质量,必须使用高压缩比环模。
压辊主要有碳化钨压辊壳、波纹式压辊壳、窝眼式压辊壳等。当压辊壳表面磨损不均匀、磨损严重时会影响颗粒质量,同时影响产量。更换环模时要切记:新模配新辊。
5 冷却
目前,冷却器一般都为逆流式冷却器,相比于卧式冷却器,需要的空气量约减少一半,同时可节约能量。
制粒后的热颗粒,温度一般在80℃以上,调质好的热颗粒水分为15%~17%,而成品颗粒水分在12.5%左右,为帮助自由水的散逸以平衡饲料水分的分布,避免后期由于水分迁移而导致的局部水分过高和饲料霉变,冷却过程中颗粒温度应降到不超过环境温度5℃范围以内。需要根据不同季节调整风机风量及冷却器料位器高度。其中要注意保证最后冷却器剩余的颗粒料有足够的冷却时间。
6 其他
6.1 保证配方的准确性,配方传送必须有反馈机制。保证配料系统称量的控制精度。
6.2 小料添加必须有监督机制,可记录可追踪,避免忘记添加或者重复添加。有些时候饲料厂客诉原因找不到,很有可能是小料称量添加出现的问题。
6.3 正确地选择更换筛片的型号,保证粉碎粒度满足料型的需求,其中粉碎粒度直径不能大于颗粒料直径的1/3。
7 小结
随着饲料产业结构升级和用户水平的逐渐提高,作为产品质量的重要组成,饲料颗粒品质的提高不仅是市场不断发展的必然趋势,也是养殖行业对饲料工业提出的迫切要求。围绕饲料颗粒品质的改善措施涵盖了营养、配方、原料、生产工艺等诸多环节,而在实际生产条件下,为塑造良好的颗粒品质,需要根据具体的配方和原料特点,采用针对性的生产工艺和措施,以此确保饲料产品具有始终如一的稳定性。
现代饲料工业的产品演化进程,主要体现出产品细分越来越多、品质标准越来越丰富、原料应用越来越多元、生产工艺越来越进步等特点,作为饲料工业的从业者,我们需要不断更新知识结构,并善于采用有价值创新的技术和手段,来更好地实现饲料工业的精细化作业。